Automation in Manufacturing: A Global Perspective on Workforce Changes
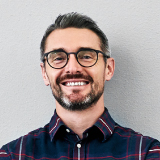
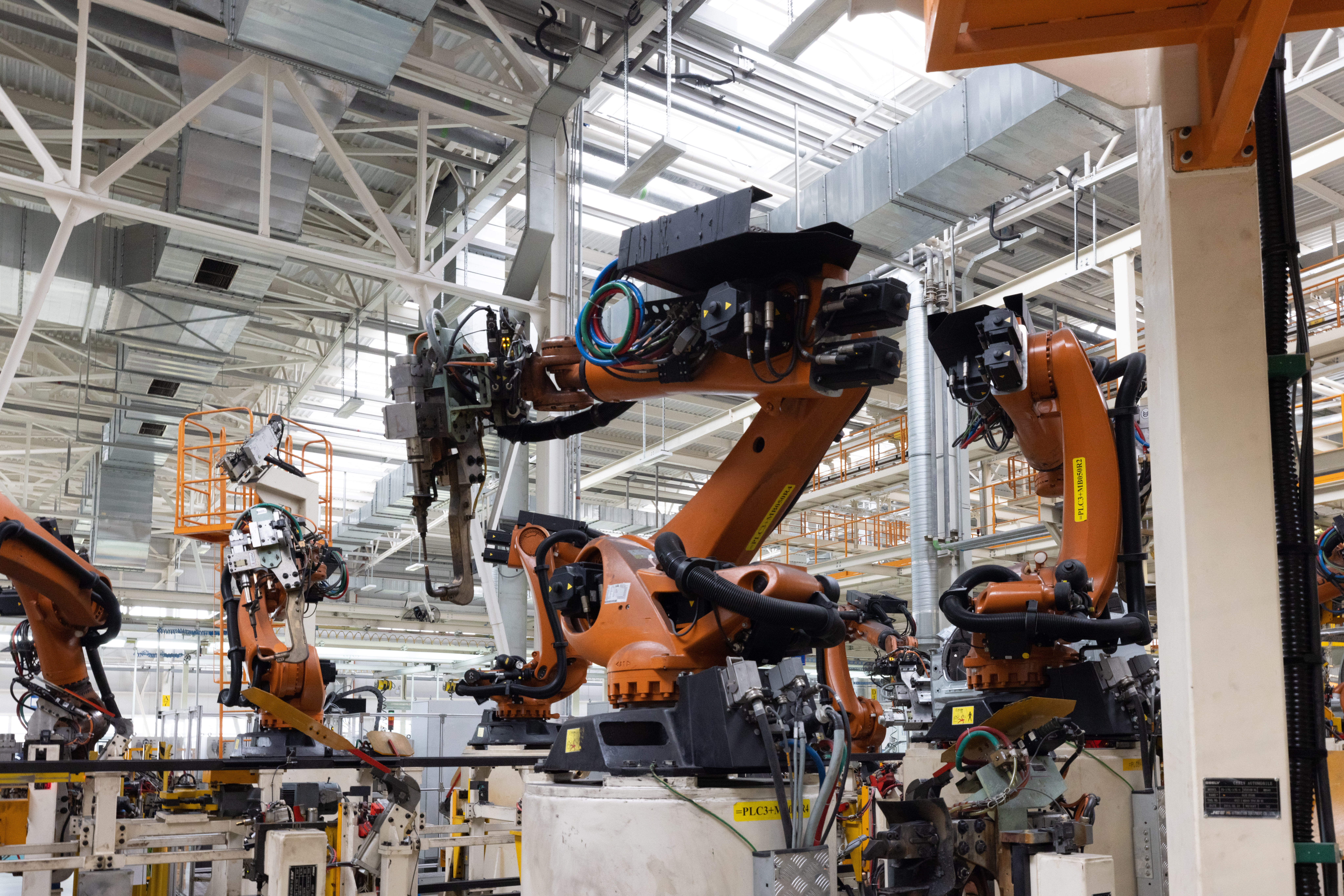
One of the biggest changes in the manufacturing sector is automation, which is changing not just the personnel but also the production methods. Understanding the global perspective on how automation is changing jobs, skills, and the very nature of work in factories worldwide is crucial as we dig into the nuances of this change.
Manufacturing has traditionally been associated with manual labor, with employees putting together goods, running equipment, and maintaining quality control. But a new era has arrived, one in which many of these jobs are being replaced by robots, artificial intelligence, and complex software. This is a fundamental shift in the way we manage labor and manufacture commodities, not just a trend.
Around the world, there are large regional differences in the deployment of automation. In affluent nations, automation is frequently viewed as a way to boost productivity and efficiency, especially in North America and some areas of Europe. These areas possess the technological infrastructure and financial means to make significant investments in automation technology. For example, German factories are increasingly adopting robotic technology to perform precise jobs so that human workers may concentrate on more intricate and creative duties. This results in higher-quality products in addition to increased productivity.
In contrast, the story is a little different in developing nations. Even while automation is becoming more popular, many manufacturers still face obstacles including restricted access to technology and a workforce that might not be skilled enough to run sophisticated machinery. Because of this, some factories in these areas could be reluctant to completely adopt automation out of concern that it will result in job losses if workers are not given proper training. But as global competition forces small businesses to take automation seriously in order to stay in business, this reluctance is progressively shifting.
The workforce's reaction to automation in production is among its most important effects. Although automation can result in job displacement, it's equally critical to acknowledge that it also opens up new opportunities. The need for qualified personnel who can maintain, program, and optimize these systems is growing as regular tasks become more automated. This change calls for a reassessment of workforce development and training initiatives in order to give employees the skills they need to succeed in an automated workplace.
In addition, new job responsibilities that did not exist ten years ago have emerged as a result of the automation of production processes. Jobs like automation engineers, data analysts, and robotics technicians are becoming more and more important in the manufacturing sector. Because these positions call for a combination of technical know-how and problem-solving capabilities, educational institutions must modify their curricula to better prepare students for the workforce of the future.
The psychological effects of automation on workers should also be taken into account. Many workers worry about their job security and the possibility that computers will replace them. A rift between management and employees may result from resistance to automation measures brought on by this worry. Companies must engage employees in the transition process and speak openly about the changes in order to allay these worries. Businesses may allay concerns and show that automation is about enhancing workers' abilities rather than replacing them by promoting a culture of cooperation and ongoing learning.
It is obvious that the manufacturing landscape will continue to change as we move to the future. With many businesses realizing the importance of resilience and adaptability in their operations, the pandemic has sped up the use of automation solutions. More manufacturers are anticipated to invest in automation as a way to future-proof their companies as a result of this trend.
Automation needs to be treated strategically, though, if it is to succeed. Businesses must perform in-depth analyses of their processes to determine which areas, without compromising the human aspect, might gain most from automation. A sustainable and productive production environment requires striking a balance between human intelligence and technology.
In conclusion, manufacturing automation offers worldwide potential as well as obstacles. technology creates the demand for a more competent workforce and opens the door for new roles, even though technology may result in job displacement. The workforce may be prepared for the future by accepting change and making investments in education and training. Fostering open communication and cooperation between companies and employees is crucial as we traverse this new terrain in order to establish a peaceful coexistence of humans and machines. Automation is a catalyst for a new era of production that may spur innovation, efficiency, and growth globally; it is more than just a change in technology.