Automation in Manufacturing: How Emerging Technologies are Reshaping the Workforce
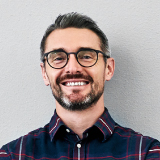
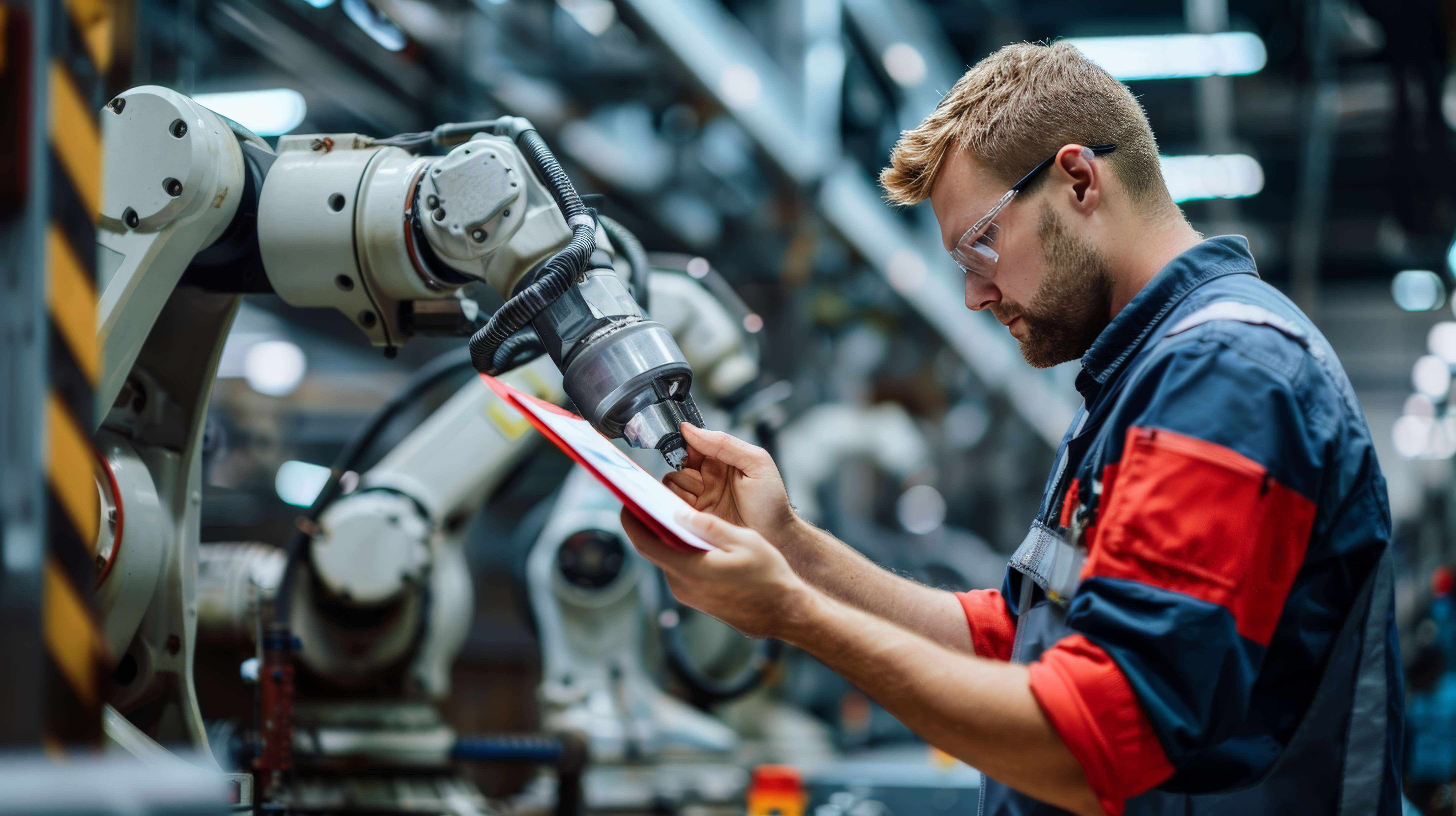
Automation in manufacturing is a revolutionary force that is changing the very makeup of the workforce; it is no longer merely a trendy term. Emerging technologies are changing the duties and responsibilities of skilled workers as well as increasing production efficiency as we approach the dawn of a new industrial era. This blog will examine the ways in which automation is transforming the industrial sector and the ramifications for both the present and future workforce.
We must first recognize the technologies behind this shift in order to comprehend the effects of automation. Manufacturing processes are undergoing a paradigm shift due to the development of robotics, artificial intelligence (AI), the Internet of Things (IoT), and machine learning. Manufacturers are able to increase overall production, decrease errors, and streamline processes thanks to these technology. This change aims to enhance human talents and foster a more collaborative work environment rather than just substituting robots for human labor.
The rise of smart factories is one of the biggest shifts brought about by automation. These facilities use networked systems and gadgets to continuously check and improve output. To anticipate maintenance requirements before catastrophic breakdowns occur, for example, IoT sensors can gather data on the performance of machinery, which can subsequently be analyzed using AI algorithms. By lowering operating expenses and downtime, this predictive maintenance strategy strengthens the production ecosystem.
However, significant concerns over the future of employment in the manufacturing industry are brought up by the rise of automation. The need for people with sophisticated technological abilities is growing as ordinary duties are increasingly replaced by machines. Previously low-skilled jobs are changing into ones that call for a deeper comprehension of technology. For instance, operators now need to be skilled in robotic system programming and troubleshooting, and data analysts are required to decipher the massive volumes of data produced by smart devices.
This change calls for a large workforce development expenditure. To give their employees the skills they need to succeed in this new climate, businesses must place a high priority on training and reskilling them. Additionally, educational institutions are essential in preparing the workforce of the future. Schools can design programs that meet industry demands by collaborating with manufacturers. This will guarantee that graduates are prepared to take on positions that require a combination of technical know-how and soft skills like critical thinking and problem-solving.
Moreover, workplace culture changes along with the manufacturing workforce. Automation makes it easier to move toward a more cooperative strategy in which machines and people collaborate side by side. This partnership increases job happiness in addition to productivity. While machines do monotonous and physically taxing work, employees may concentrate on higher-value jobs that call for creativity and critical thought. A more engaged workforce is made possible by this mutually beneficial connection, where workers feel appreciated and empowered to contribute to the success of their company.
This change is not without its difficulties, though. As automation develops, there is a growing concern about job displacement. Even though it's possible that some vocations could become obsolete, it's important to concentrate on the potential presented by this technological advancement. Historically, technology innovations have created more jobs than they have lost, according to research. For individuals who are flexible, new career paths are opening up in fields like data analysis, AI development, and robotics maintenance.
Businesses that adopt automation are also better equipped to compete in a global marketplace. Manufacturers are able to provide competitive prices and superior products due to increased efficiency and decreased production expenses. With successful manufacturers able to invest in growth, innovation, and staff expansion, this has a positive knock-on effect on the economy in addition to improving the bottom line.
The use of developing technologies in manufacturing will surely continue to develop as we move forward. A proactive approach to workforce development and cooperation between technology and human skill sets are essential for managing this transition. Manufacturers may guarantee that their staff stays relevant and capable of prospering in a technologically evolved environment by making training investments and cultivating an adaptable culture.
To sum up, factory automation is drastically changing the nature of the labor. Emerging technologies are redefining occupations, opening up new opportunities, and improving human-machine collaboration rather than just replacing them. Manufacturers may fully utilize automation by embracing this shift and making investments in worker development, guaranteeing a more promising and inventive future for the sector. Manufacturing is entering a new era that blends the greatest technological advancements with the inestimable worth of human creativity.