Automation Trends: How Robotics is Changing Manufacturing Across Continents
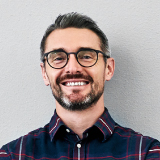
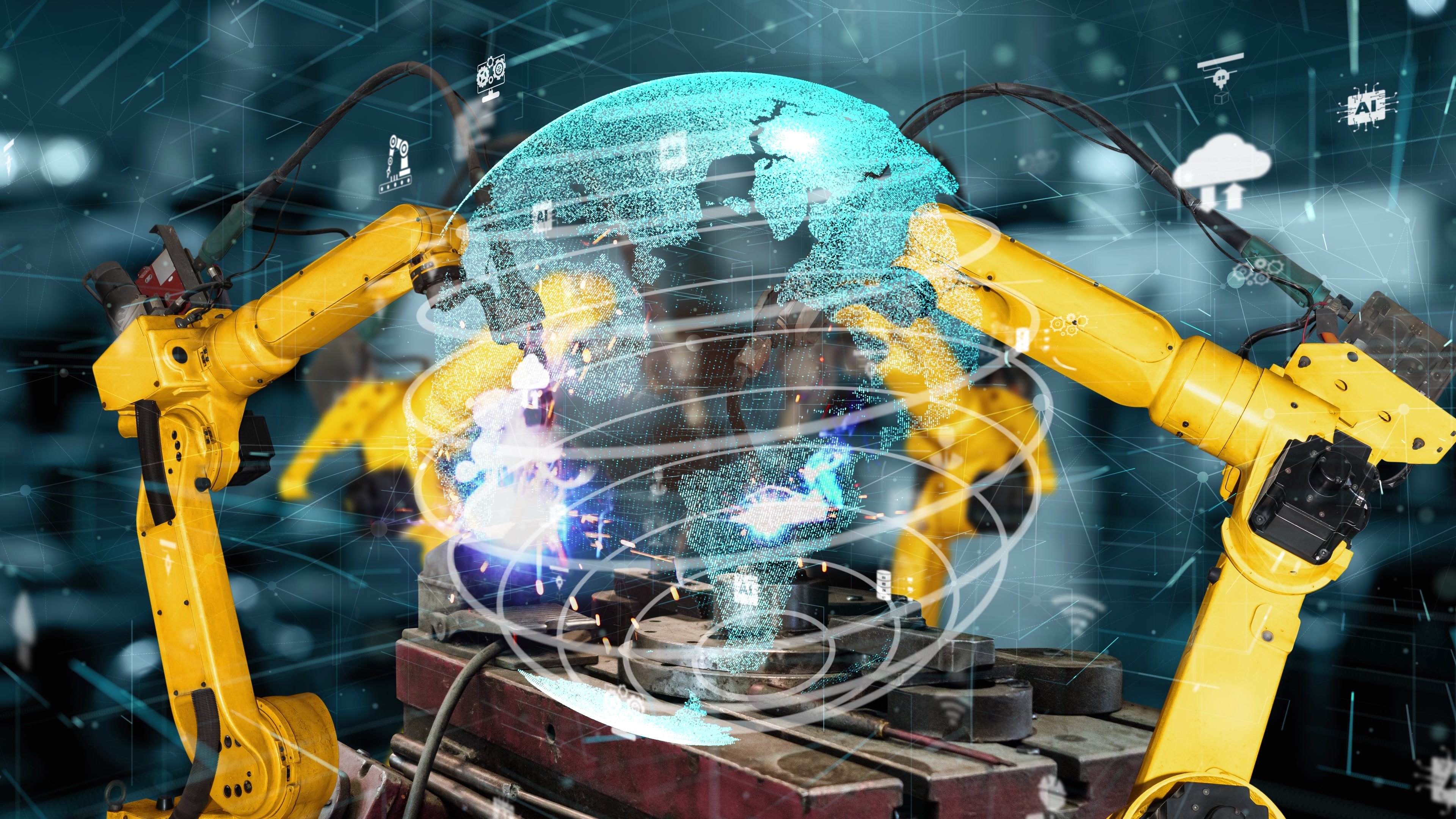
The manufacturing sector has significantly changed, mainly due to the technological innovations constant infusion of robotics into production processes. Having worked for over 10 years as a blog writer content writer, I know how automation trends are changing the global scope of industries. This article will focus on the impact of robotics on the manufacturing industry across different continents improving productivity, safety and creating more advanced products.
Robotic devices do not exist in the sphere of science fiction anymore. It became a part of a modern manufacturing industry. Whether it is North America’s car production or Asia’s electronics assembly, robots are quite efficiently adjusting the operations and procedures and assisting manufacturers to appeal to the needs of the global market. As we explore the different dimensions of this metamorphosis, it is equally important to identify key trends that will be critical to the future of manufacturing.
The introduction of collaborative robots or cobots is one of the most significant trends in the evolution of manufacturing automation. Unlike conventional industrial robots that command a cell or factory on their own, cobots are designed to function within a human-staffed workspace. This collaboration not only boosts the overall output but also improves the environment within which operations are conducted. Due to cobots, human workers do not need to perform monotonous or dangerous jobs, which gives them more creative and sophisticated tasks. This model is ideal in areas experiencing a chronic shortage of labor because it allows organizations to function effectively even without a lot of manpower.
The rise of collaborative robots has led to another trend that shows increasing promise the use of AI and machine learning in robotics. These technologies enable robots to acquire fundamental aspects from their surroundings, adjust to different environments, and—perhaps most importantly—make real-time decisions. For example, AI robots have vast amounts of production data that can be utilized to improve workflows, reduce maintenance, and avoid unplanned stoppage. Such intelligence is apparently changing how manufacturers think about issues and make decisions, improving their operational flexibility and responsiveness.
On a global scale, producers are also adopting IoT in their robotic systems. By attaching robots to a network of machines, it becomes possible to monitor activities, collect information, and analyze operations. The ability to reach equipment over the networks will facilitate predictive maintenance and make unscheduled breakdowns minimal, and the workflow is smooth. In Europe, there has been a steady rise in the number of robots that are IoT enabled for particular tasks such as improving supply chain transparency and enhancing operational effectiveness which translates to cost reduction and increased competitiveness.
Further, sustainability is also emerging as a factor that is supporting automation of the manufacturing industry. Since companies continue to face scrutiny over their carbon footprint, some have opted for robots as a remedy. Automated systems enhance the efficiency of resource use, reduce waste, and lower the cost of energy. For example, robotic arms replace hands and highly reduce the amount of material that is salvaged. Such a sustainable approach appeals to the needs of the end-users as well as the stakeholders and builds a brand image within the industry as a responsible actor.
The geographical aspect of the deployment of the robotics systems exhibits significant context-specific differences between regions and can be attributed to local economy, labor, as well as the existing technological ecosystem. In North America, for instance, the automotive sector has emerged as the pioneering industry in the robotic automation as the manufacturers have consistently adopted robust robotic systems to enhance their production levels and to stay competitive in the market. On the other Hand, Asia, more specially, China and Japan see a big market in robotics as countries are looking towards mass quality production. New robotics solutions are also emerging in these regions’s start-up innovations to meet different manufacturing requirements.
In Europe, the trend now is to move the robotic systems to fusion with digital technologies. The European Union has also launched funds to support smart and advanced manufacturing practices appealing to an integration of robotic, AI, IoT, and other advanced technologies. In addition, cooperation between industries and research and development in Europe aims to be at the forefront in the production of world-class robotic technologies that can be deployed in different industries.
Nonetheless, the shift towards automation of manufacturing processes does not come without its challenges. Job loss due to robots doing the works that were once carried out by people has become a serious concern. To address this concern, businesses must make a commitment to retraining and upskilling their people in order to enable them to take up more challenging jobs. Because of the willingness to learn and adapt, manufacturers can accomplish in having their teams ready to operate in a world where there is a lot of automation.
To summarize, the use of robots in manufacturing has a great influence in the manufacturing processes that extends well into the future. For instance, as the trends of collaborative robots, integrated Artificial Intelligence ,Internet of Things, and sustainability change the scope of the industry, the manufacturing industry is preparing for a shift that will greatly increase effectiveness and open up possibilities. I think it is important for all organizations to keep watch of these trends fast, given that the global marketplace is swiftly changing. By embracing the processes of automation, manufacturers can not only make their operations more efficient but can also enhance the type of future that is bright and sustainable.